AN230371 High voltage subsystem (HVSS) in PSOC™ HV PA family

About this document
Scope and purpose
This application note introduces you to the high-voltage subsystem (HVSS) of PSOC™ 4 HV precision analog (PA) family. This application note also guides you to develop HVSS hardware and firmware design for battery monitoring application.
Intended audience
This document is intended for hardware and firmware design engineers.
Introduction
This application note provides an overview of the high-voltage subsystem (HVSS) with the CY8C41xxLCE-HV4xx series from the PSOC™ 4 high voltage (HV) precision analog (PA) family. PSOC™ 4 HV PA is a fully integrated programmable embedded system for battery monitoring and management. The system features an Arm® Cortex® M0+ processor and programmable and reconfigurable analog and digital blocks. To get a better understanding of the HVSS functionality described and terminology used in this application note, it is a good idea to read the "Section 22: High-voltage subsystem" chapter of the
architecture reference manual
.
HVSS overview
The PSOC™ 4 HV PA high-voltage subsystem (HVSS) contains a series of analog circuits used in battery monitoring and management applications. The applications are directly connected to an automotive battery and operates up to 42 V. The HVSS has the following features:
HVSS circuits operate directly off 12 V/24 V automotive battery (tolerates up to 42 V)
A linear regulator powered by the automotive battery voltage producing 3.3 V (HVREG)
Output voltage accuracy: 2.7 V to 3.6 V
Input voltage range: 3.6 V to 42 V
Output current capability: 30 mA
Low current consumption for always on: 20 µA maximum
Power good function
A LIN physical interface transceiver (LIN PHY)
Data rates up to 20 kbps with high EM noise immunity
Positive/negative DC tolerance for LIN pin: –27 V to 42 V
Sleep mode current consumption: IVBAT + IVDDD = 10 µA maximum
Programmable slew rate control: 1.0/1.5/2.0 V/us at VBAT = 12 V
Dominant timeout and LIN wakeup interrupt timers
A set of input voltage dividers (VDIVIDER) providing attenuated signals to ADCs
Dividers attenuate the input by a factor of 16x or 24x
1.2 V full-scale outputs from an input of 19.2 V (16x) or 28.8 V (24x)
An AHB bus interface and control/status registers
Interrupt logic
shows the block diagram for the HVSS.
Figure 1. HVSS block diagram
HV regulator (HVREG)
The HVREG is the high-voltage regulator with self-startup from the battery without a reference voltage; it provides 3.3 V to VDDD and VDDA as the chip supply. It also contains a power good function and Zener diode on the output pin for overvoltage protection. The HVREG operates with stability against automotive battery voltage transient events, keeping the output voltage between 2.7 V to 3.6 V even if the VBAT pin drops down to 3.6 V in cold cranking or rises up to 42 V in a load dump surge.
LIN PHY
The LIN PHY is the interface between the local interconnect network (LIN) protocol controller and the physical bus in a LIN, which meets the requirements of LIN standard 2.2 A and is backward compatible with LIN 2.0. It supports data rates of 1 to 20 kbps. Non-LIN fast slew rates are available providing 100 kbps data rates for fast downloads, for factory and field flash program updates using the LIN pin.
HV ADC voltage dividers (VDIVIDER)
The VDIVIDER is a voltage divider used on the VSENSE and VDIAG pins to scale the battery voltage to levels compatible with on-chip ADCs so that battery voltages can be measured. In typical battery monitoring and management applications, the VSENSE input is normally connected directly to the battery with a series 2.2 kΩ resistor to measure battery voltage. VDIAG can be used to measure the voltage at other locations such as the ECU or other loads where monitoring is desired. The external 2.2 kΩ resistors in series with voltage sources limit the current during ESD and transient voltage events.
HVREG
Block description
shows the HVREG block architecture and function diagram. The HVREG generates a nominal 3.3 V output voltage with loads up to 30 mA from an external supply voltage input of 3.6 V to 42 V. The regulator maintains the output voltage from 3 V to 3.6 V when the supply voltage is greater than 4 V and may drop to 2.7 V when the supply is between 3.6 V to 4 V. In normal operation, the external automotive battery voltage is typically 12 V or higher but can drop as low as 4.5 V during cold cranking. However, the voltage at the V
BAT
pin can go as low as 3.6 V due to a reverse polarity protection diode and an EMI filter resistor.
This regulator provides 3.3 V
V
DDD
(and 3.3 V
V
DDA
), which are used to power the chip, including the digital regulators which then generate
V
CCD
(1.8 V) supplies. This regulator is always powered on.
Figure 2. HVREG block architecture and function diagram
HVREG input pins
vddd_in is an analog input signal pin to monitor the
V
DDD
voltage level with the power good circuit (PG). This pin is connected to the output
V
DDD
at the appropriate place in the chip to monitor the drop in
V
DDD
.
HVREG output pins
vddd is the output pin of this regulator, a nominal 3.3 V regulated voltage with loads up to 30 mA. This output drives the device’s
V
DDD
and
V
DDA
, and through the GPIO can drive external loads. The vddd pin is always ON after startup.
pg_hv
is the output pin of the power good circuit in HVREG. HVREG monitors the
V
DDD
output voltage through the
vddd_in
pin. When
V
DDD
is lower than 2 V,
pg_hv
provides a LOW. Thus, this output signal can work as the reset signal of the entire device in the voltage range lower than Vddd = 2.0 V.
Operating voltage
and
Table 2
show the HVREG absolute maximum ratings and operating conditions. See
PSOC™ 4 HV PA datasheet
for more information.
Parameter | Description | Min. | Typ. | Max. | Units | Details/conditions |
---|---|---|---|---|---|---|
V BAT | Supply voltage V BAT | −0.3 | – | 42 | V | |
I BAT | V BAT supply current | – | – | 160 | mA | |
I BATABSDC | V BAT supply current, long-term average | – | – | 40 | mA |
Parameter | Description | Min | Typ | Max | Units | Details/conditions |
---|---|---|---|---|---|---|
V BAT | Battery supply voltage V BAT | 3.6 | – | 28 | V | |
V DDA | Analog regulator voltage | 3 | 3.3 | 3.6 | V | |
I DDA | Analog regulator current | – | N/A | – | – | Not to be used off-chip |
V DDD | Digital regulator voltage, V BAT > 4 V | 3 | 3.3 | 3.6 | V | |
V DDD | Digital regulator voltage, 4 V≥ V BAT ≥3.6 V | 2.7 | – | 3.6 | V | |
I DD | Digital regulator current | – | – | 30 | mA | Core, GPIO, and external loads |
VDIVIDER
Block description
VDIVIDER is used to scale the high-voltage analog inputs down to levels compatible with the ADC full-scale input voltage (1.2 V). These programmable dividers support two voltage scales – 16x (19.2 V full scale) or 24x (28.8 V full scale). Each divider can be independently enabled or disabled. The divider generates a differential signal for the ADC with the bottom of the divider referenced to vdiv_ret.
shows the block diagram of the VDIVIDER.
Figure 3. VDIVIDER block diagram
VDIVIDER input pins
pg_hv
is the reset signal input pin. While this pin is LOW, the level shift circuit is in reset;
vs_div0/vs_div1
outputs "L" regardless of the
rdiv_en<1:0>
voltage level. The voltage level of this bus signals is
V
DDD
.
rdiv_en<1:0>
is an input bus for enabling the resistor dividers of the vsense and
vdiag
inputs. When either signal is set to "L", the corresponding resistor ladder is opened and its output becomes low. The voltage level of this bus signals is
V
CCD
.
rdiv_scale<1:0>
is an input bus to set the voltage attenuator ratio to either 1/16 or 1/24. The voltage level of this bus is
V
CCD
.
VDIVIDER output pins
vs_div0/vs_div1
are output pins of the divided
vsense/vdiag
signals. The voltage level of this bus is
V
DDD
.
Operating voltage
and
Table 4
show the VDIVIDER absolute maximum ratings and operating conditions. See
PSOC™ 4 HV PA datasheet
for more information.
Parameter | Description | Min. | Typ. | Max. | Units | Details/conditions |
---|---|---|---|---|---|---|
V SHV | V SENSE /V DIAG ADC sense voltage | −0.3 | – | 42 | V | |
V SHV | V SENSE /V DIAG ADC sense voltage | −40 | – | 42 | V | With external 2.2 kΩ resistor |
I SH | V SENSE /V DIAG current | −20 | – | 1 | mA | Forced externally |
Parameter | Description | Min. | Typ. | Max. | Units | Details/conditions |
---|---|---|---|---|---|---|
V SENSE | V BAT sense voltage | 3.6 | – | 28 | V | |
V DIAG | V DIAG sense voltage | 3.6 | – | 28 | V | |
I SENSE | V SENSE /V DIAG current | 5 | 20 | μA | ||
V RMEAS | HV measurement range | 0 | – | 28 | V | With HVATTEN = 24 |
V RMEASLV | LV measurement range | 0 | – | 1.2 | V | |
V RES | Resolution | – | 0.293 | – | mV | 0 V to 18 V input range (Rdiv=16) |
V RES | Resolution | – | 0.4 | – | mV | 0 V to 28 V input range (Rdiv=24) |
LIN PHY
Block description
The LIN driver includes slew control to maintain a consistent duty cycle over a range of loads. It also includes turn-on/turn-off control to round the edges and minimize the EMI. Large amounts of RF energy can be present on the LIN bus; the driver must remain functional in the presence of this energy, which requires special attention to the design of the feedback circuits so they do not saturate in the presence of RF energy.
LIN receiver thresholds are specified in relation to the supply voltage, VBAT. A comparator with voltage dividers sets the receiver threshold and scales the bus voltages to appropriate levels. Noise filtering is needed to prevent the RF energy and brief transients from disturbing the communication.
The LIN specification has certain isolation requirements to ensure that the LIN bus is not compromised by certain faults, and that the loss of supply voltage or the ground of a slave node does not affect the LIN communication between other nodes. To address this requirement, the following are introduced:
Reverse protection diodes in series with pull-up resistors
A diode in series with the open-drain pull-down resistor to prevent powering the components from the LIN bus and/or excessively loading the LIN bus and disrupting the communication
shows the LIN PHY transceiver block diagram.
Figure 4. LIN PHY block diagram
LIN PHY input pins
Pin | Description |
---|---|
lin_mode<2:0> | Input to change the LIN PHY function mode |
txd | Data input signal, giving the drive state intended at the LIN pin in LIN PHY transmit mode |
txd_en | Input signal to mask the
signal. When
is "L", the transmitter is controlled so that the
input is ignored and the LIN pin becomes "recessive" (weak pull-up). |
sl_round | Input configuration signal to tune the falling slew rate of LIN waveform. When the rounding mode is selected, the falling slope of the LIN bus waveform will be more moderate for lower EMI emission. |
LIN PHY output pins
Pin | Description |
---|---|
Lin | Input/output pin for LIN PHY transceiver. The block's transmitter can drive this pin. The receiver uses it as an input. This pin requires a positive/negative tolerance from −27 V to 42 V (to account for a "lost ground" mode that can give negative inputs, and battery surge cases for the high positive voltages). |
rxd | Output of the LIN PHY receiver. The voltage level of this signal is V CCD and reflects the state of the LIN pin. |
Operating conditions
and
Table 6
show the LIN PHY absolute maximum ratings and operating conditions. See
PSOC™ 4 HV PA datasheet
for more information.
Parameter | Description | Min. | Typ. | Max. | Units | Details/conditions |
---|---|---|---|---|---|---|
V LIN | LIN pin voltage | −27 | – | 42 | V | |
I LIN | LIN pin current | – | – | 200 | mA | |
t SCLIN | Short circuit tolerance: LIN | – | – | 60 | min | V BAT = LIN: 3.6 V to 28 V |
– | – | 500 | ms | V BAT = LIN: 28 V to 42 V |
Parameter | Description | Min. | Typ. | Max. | Units | Details/conditions |
---|---|---|---|---|---|---|
V BAT_LIN | V BAT range for LIN communications | 7 | – | 28 | V | LIN2.2 A parameter 10 |
V LIN | LIN output voltage | 6 | – | 28 | V | |
R LIN,PU | LIN pull-up resistor | 20 | 30 | 47 | kΩ | |
I BUS_LIM | LIN output current | 40 | – | 200 | mA | Param 12 |
V BUSdom | Receiver dominant state | – | – | 0.4 | V BAT | Param 17 |
V BUSrec | Receiver recessive state | 0.6 | – | – | V BAT | Param 18 |
V BUScnt | Receiver center voltage | 0.475 | 0.5 | 0.525 | V BAT | Param 19 |
V BUShys | Receiver hysteresis | – | – | 0.175 | V BAT | Param 20 |
V OH | Bus transmitter recessive output voltage | V BAT -2 | – | V BAT | V | Not a LIN 2.2 A specification |
V OL | Bus transmitter dominant output voltage ( V BAT = V BUS =7 V) | – | – | 1.2 | V | RL = 500 Ω (IOL<12 mA) |
V OL | Bus transmitter dominant output voltage ( V BAT = V BUS =18 V) | – | – | 2 | V | RL = 500 Ω (IOL<32 mA) |
V SerDiode | Voltage drop at external series Diodes | 0.4 | 0.7 | 1 | V | Param 21 |
R LIN,PU | Internal slave pull-up Resistor | 20 | 30 | 47 | kΩ | Param 26 (RSLAVE) |
R LIN,PD | Internal pull-down resistor for Diagnosis | 20 | 30 | 47 | kΩ | Not a LIN 2.2 A specification |
LIN physical layer specification overview
LIN is a low-cost serial communication protocol, which has been standardized by the LIN consortium. The main properties of LIN are:
Single master with one or more slaves
Speeds up to 20 kbps
Single-wire implementation
Low cost silicon implementation based on common UART/SCI interface hardware or equivalent software/hardware state machine
The physical interface is a single-wire (not including ground) using a physical layer interface (PHY). The LIN PHY has two states: the recessive state where the LIN bus is pulled up close to the vehicle battery voltage (a reverse protection diode causes a small voltage drop) and a dominant state, which is essentially 0 V.
shows an overview of a LIN network.
Figure 5. LIN overview
Each node on the LIN network uses a LIN PHY (transceiver) to communicate over the network. The LIN physical layer is independent of the higher LIN protocol layers including master and slave operation. There are no differences between master and slave transceivers. Each LIN network can have up to 16 nodes. The PHY has a transmitter section, which includes the open-drain pull-down transistor and gate driver circuitry, a receiver, and a small pull-up resistor.
The master node includes a termination resistor that ranges from 500 to 1000 Ω depending on network speed and bus length (up to 40 m). The LIN PHY specification specifies network loads of 1000 Ω pull-up with 1 nF bus load capacitance, 680 Ω with 6.8 nF, and 500 Ω with 10 nF. All nodes include a nominal 30 kΩ nominal pull-up resistor; this is intended to compensate for increasing node capacitance (typically ~270 pF/node) to maintain approximately the same pull-up resistor to load capacitance (R × C) time constant as nodes are added. Typically used network speeds are either 10 kbps or 20 kbps.
HVSS firmware configuration
Infineon provides the sample driver library (SDL) including startup code as sample firmware. The SDL provides a simple interface to access various peripherals and is used for system validation, hardware bring-up, benchmarks, feasibility studies, and demos. The SDL integrates device header files, startup code, and peripheral drivers. The SDL contains a set of firmware drivers that provide APIs for accessing device-specific resources and example for each peripheral. See AN230264 - Getting started with PSOC™ 4 HV PA family
[1]
for detailed SDL information.
The SDL should not be used for production purposes because it is not qualified with any automotive standards.
The following sections explain the details of the API and code examples for HVSS.
Peripheral drivers
Peripheral drivers are a set of firmware drivers that provide APIs for accessing the hardware. These APIs perform initialization and control activities of each peripheral.
lists and describes the interface to each HVSS function. The peripheral drivers of HVSS are located in the following SDL path:
C:/<user path>
PSoC_Sample_Driver_Library_x.x.x\psoc4hvXXXk\src\drivers\hvss
See
API details
for more information.
Function | Description |
---|---|
| |
Cy_Hvss_Init | Configures the HVSS module, which includes RDIV (resistor attenuation) and LIN-PHY configuration. This function should be called before using the LIN communication functions. |
Cy_Hvss_DeInit | De-initializes both the LIN module and the RDIV |
| |
Cy_Hvss_Hvreg_GetStatus | Gets the status of the HVSS regulator |
Cy_Hvss_Rvid_EnableVS0 | Enables VS0 in resistor attenuator control (RDIV) |
Cy_Hvss_Rvid_DisableVS0 | Disables VS0 in RDIV |
Cy_Hvss_Rvid_EnableVS1 | Enables VS1 in RDIV |
Cy_Hvss_Rvid_DisableVS1 | Disables VS1 in resistor attenuator control (RDIV) |
Cy_Hvss_Rvid_SetPowerMode | Sets the power domain mode in RDIV |
Cy_Hvss_Rvid_GetPowerMode | Gets the power domain mode of RDIV |
Cy_Hvss_Rvid_SetAttenuationVS0 | Gets VS0 attenuation of RDIV |
Cy_Hvss_Rvid_GetAttenuationVS0 | Gets VS0 attenuation of RDIV |
Cy_Hvss_Rvid_SetAttenuationVS1 | Gets VS1 attenuation of RDIV |
Cy_Hvss_Rvid_GetAttenuationVS1 | Gets VS1 attenuation of RDIV |
Cy_Hvss_LinPhy_SetRxdPin | Sets the status of the LIN-PHY RxD pin |
Cy_Hvss_LinPhy_GetRxdPin | Gets the status of the LIN-PHY; this will give the current status of the LIN RxD pin |
Cy_Hvss_LinPhy_EnableWakeupTimer | Enables the LIN-PHY wake-up timer; required LIN compatibility in DS mode. |
Cy_Hvss_LinPhy_DisableWakeupTimer | Disables the LIN-PHY wake-up timer |
Cy_Hvss_LinPhy_GetWakeupTimerStatus | Gets the status of the LIN-PHY wakeup timer; will give the timer count if running |
Cy_Hvss_LinPhy_EnableFaultTimer | Enables the LIN-PHY fault timer; required LIN compatibility in DS mode |
Cy_Hvss_LinPhy_DisableFaultTimer | Disables the LIN-PHY fault timer |
Cy_Hvss_LinPhy_GetFaultTimerStatus | Gets the status of the LIN-PHY fault timer; will give the timer count if running. |
Cy_Hvss_LinPhy_SetPhyMode | Sets the LIN-PHY mode |
Cy_Hvss_LinPhy_GetPhyMode | Gets the current LIN-PHY mode |
Cy_Hvss_LinPhy_SetPhySlRound | Sets the SL round value of the LIN-PHY for lower EMI |
Cy_Hvss_LinPhy_GetPhySlRound | Gets the SL round mode of the LIN-PHY |
Cy_Hvss_LinPhy_SetPhyInterface | Sets the internal or GPIO connection of the LIN-PHY through the HSIOM |
Cy_Hvss_LinPhy_GetPhyInterface | Gets the connection interface of the LIN-PHY through internal or GPIO |
Cy_Hvss_LinPhy_EnablePhy | Enables the LIN-PHY |
Cy_Hvss_LinPhy_DisablePhy | Disables the LIN-PHY |
Cy_Hvss_LinPhy_GetPhyStatus | Gets the LIN-PHY status: 1- enabled 0 - reset (RxD pin is High-Z) |
Cy_Hvss_LinPhy_ClearInterrupt | Clears the interrupt from the LIN_INTR register |
Cy_Hvss_LinPhy_SetInterrupt | Sets the interrupt in the LIN_INTR register |
Cy_Hvss_LinPhy_GetInterruptMask | Returns the interrupt mask from the LIN_INTR_MASK register |
Cy_Hvss_LinPhy_SetInterruptMask | Sets the interrupt mask in the LIN_INTR_MASK register |
Cy_Hvss_LinPhy_GetInterruptStatusMasked | Returns the masked status from the LIN_INTR_MASKED register |
Cy_Hvss_LinPhy_SetWakeupInterruptMask | Sets the wakeup interrupt status masked the in LIN_INTR_MASK register |
Cy_Hvss_LinPhy_ClearWakeupInterruptMask | Clears the wakeup interrupt status masked in the LIN_INTR_MASK register |
Cy_Hvss_LinPhy_SetFaultInterruptMask | Sets the fault interrupt status masked in the LIN_INTR_MASK register |
Cy_Hvss_LinPhy_ClearFaultInterruptMask | Clears the fault interrupt status masked in the LIN_INTR_MASK register |
Startup/initialization sequence
shows the flowchart for HVSS settings.
Figure 6. HVSS startup flowchart
The
Table 8
and
Table 10
steps are recommended when using HVSS:
Step number | Step | Description | Values |
---|---|---|---|
1 | RDIV enable | Enable the resistor dividers of the vsense and vdiag inputs. | Block: VDIVIDER Pin name:
Function:
|
2 | RDIV active enable | Select power modes where RDIV is enabled: 0=Enable in Active and Deep-Sleep modes 1=Enable in Active mode only | Block: VDIVIDER Pin name: none Function:
|
3 | RDIV scale enable | Set the voltage attenuator ratio to either 1/16 or 1/24: 0=16X attenuation 1=24X attenuation | Block: VDIVIDER Pin name:
Function:
|
4 | LIN mode set | Change the LIN PHY function mode (See Table 9 ) | Block: LIN PHY Pin name:
Function:
|
5 | LIN EMI value set | Set the SL round value of the LIN-PHY for lower EMI: 0=Normal 1=More moderate (rounded) for lower EMI | Block: LIN PHY Pin name:
Function:
|
6 | LIN PHY interface set | Set the internal or GPIO connection of the LIN-PHY through the HSIOM: 0= Primary interface (connected to the internal LIN controller through HSIOM) 1= Alternate interface (connected to GPIOs through HSIOM) | Block: LIN PHY Pin name: none Function:
|
7 | LIN enable | Enable the
. enable function:
disable function:
| Block: LIN PHY Pin name:
Function:
or
|
8 | LIN wakeup timer enable (if applicable) | a. Enable the
wake-up timer b. Set the value of the
wake-up timer (Number of
edges before wakeup interrupt is triggered) | Block: LIN PHY Pin name: none Function:
|
9 | LIN fault timer enable (if applicable) | a. Enable the
fault timer. b. Set the value of the
fault timer (number of
edges before a fault interrupt is triggered) | Block: LIN PHY Pin name: none Function:
|
Input | Output (driver) | |||||||
---|---|---|---|---|---|---|---|---|
State No. | LIN transceiver function | LIN_MODE[2:0] | Receiver | Slew control | Slew rate setting | txd = 1 | txd = 0 | Pull-up |
0 | Disable | 000 | Off | No | _ | High-Z | High-Z | Off |
1 | Sleep | 001 | On (Low power) | No | _ | Recessive | Recessive | On |
2 | Standby | 010 | On | No | _ | Recessive | Recessive | On |
3 | Diagnosis | 011 | On | No | _ | Recessive | Low (weak) | On/Off |
4 | Normal mode | 100 | On | Yes | 1.0 V/µs | Recessive | Low (dominant) | On |
5 | 101 | On | Yes | 1.5 V/µs | Recessive | Low (dominant) | On | |
6 | 110 | On | Yes | 2.0 V/µs | Recessive | Low (dominant) | On | |
7 | Fast mode | 111 | On | No | _ | Recessive | Low (dominant) | On |
Step | Description | |
---|---|---|
1 | RDIV control register to default | Set all bits of register to 0 "RDIV enable", "RDIV active enable" and "RDIV scale enable" |
2 | LIN PHY control register to default | Set all bits of register to 0 "LIN enable", "LIN PHY interface", "SL round" and "LIN mode" |
3 | LIN PHY timers to default | Set all bits of register to 0 "Wakeup timer" and "Fault timer" |
4 | LIN interrupt request register to default | Set all bits of register to 0 "Wakeup interrupt" and "Fault interrupt" |
5 | LIN interrupt set register to default | Set all bits of register to 0 "Wakeup interrupt" and "Fault interrupt" |
6 | LIN interrupt mask register to default | Set all bits of register to 0 "Wakeup interrupt" and "Fault interrupt" |
Selecting the external components
HVREG
Schematic example
shows an example HVREG schematic;
Table 11
shows an example of external components.
Figure 7. HVREG schematic example
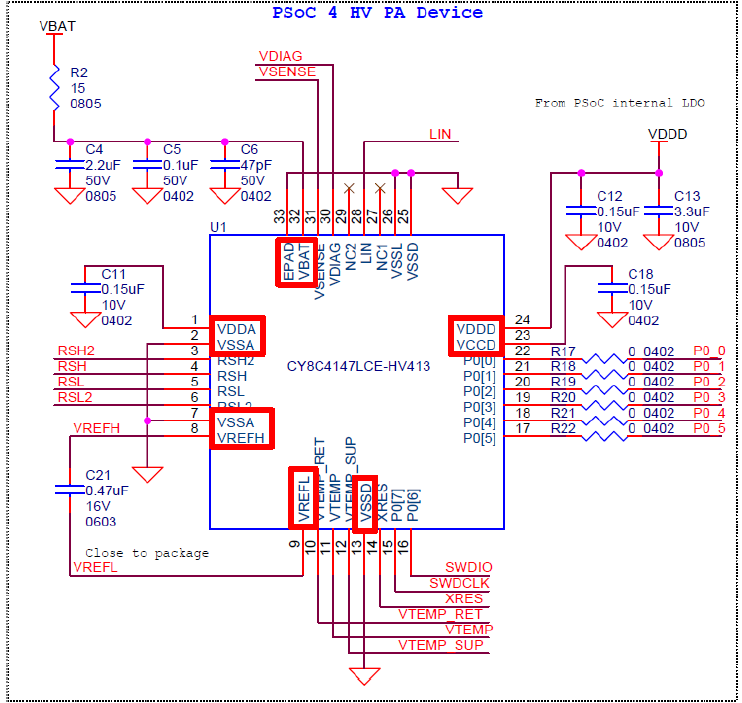
Symbol | Overview | Parameter | ||
---|---|---|---|---|
Value 1 | Value 2 | Remark | ||
C4 | Decoupling/smoothing capacitor for the high-voltage domain | 2.2 μF X7R | > 50 V | |
C5 | Decoupling capacitor for the high-voltage domain | 0.1 μF X7R | > 50 V | |
C6 | Capacitor for the external noise filter | 47 pF C0G | > 50 V | |
C11 | Decoupling capacitor for the VDDA domain | 0.15 μF X7R | > 6.3 V | |
C12 | Decoupling capacitor for the VDDD domain | 0.15 μF X7R | > 6.3 V | |
C13 | Decoupling/smoothing capacitor for the VDDD domain | 3.3 μF X7R | > 6.3 V | |
C18 | Decoupling capacitor for the VCCD domain | 0.15 μF X7R | > 6.3 V | |
C21 | Reference capacitor for the VREF domain | 0.47 μF X7R | > 6.3 V | |
R2 | Input filter resistor for the high-voltage domain | Typ 15 Ω (7.5~15 Ω) | > 0.25 W |
Layout example
shows an example of the HVREG layout.
Figure 8. HVREG layout example
Follow these guidelines for the PCB power supply circuit on the PSOC™ 4 HV PA device:
Place the V BAT input capacitors C4, C5, and C6 as close as possible to the VBATpin. Place C6 closer to the VBAT pin, followed by C5 and C4. Place the R2 resistor for the input filter next to C4 and draw the layout as linear as possible. If the board has a GND plane, provide a through hole (via) near this capacitor
Place the VDDA capacitor (C11) as close as possible to the VDDA pin and the VSSA pin to minimize the current loop from VDDA to VSSA. If the board has a GND plane, provide a through hole near the VSSA pin of this capacitor.
Place the VDDD capacitors (C12 and C13) as close as possible to the VDDD pin to minimize the current loop from VDDD to VSSD. Place C12 closest to VDDD, followed by C13. If the board has a GND plane, provide a through hole connecting to the GND plane, near this capacitor.
Place the VCCD capacitor (C18) as close as possible to the VCCD pin to minimize the current loop from VCCD to VSSD. If the board has a GND plane, provide a through hole connecting to the GND plane, near this capacitor.
Place the reference voltage capacitor (C21) as close as possible to the VREFH and VREFL terminals. It is recommended to place the VREFH and VREFL traces diagonally, so that they have the same length. Place this capacitor on the same PCB layer as the device and avoid using through holes.
Provide a through hole for GND plane connection near each GND pin (VSSD, VSSA, VSSL).
When using LIN, place the LIN capacitor near the LIN and VSSL pins.
Provide a GND plane on the mounting surface of this IC. To effectively dissipate the heat from the QFN-32 package, it is recommended to provide a thermal via in the footprint of the thermal pad
See
AN230370
for schematic and layout examples of each sensor input (current/voltage/temperature).
VDIVIDER
Schematic example
shows an example of the VDIVIDER schematic;
Table 12
shows an example of external components.
Figure 9. Schematic example of voltage sensor line
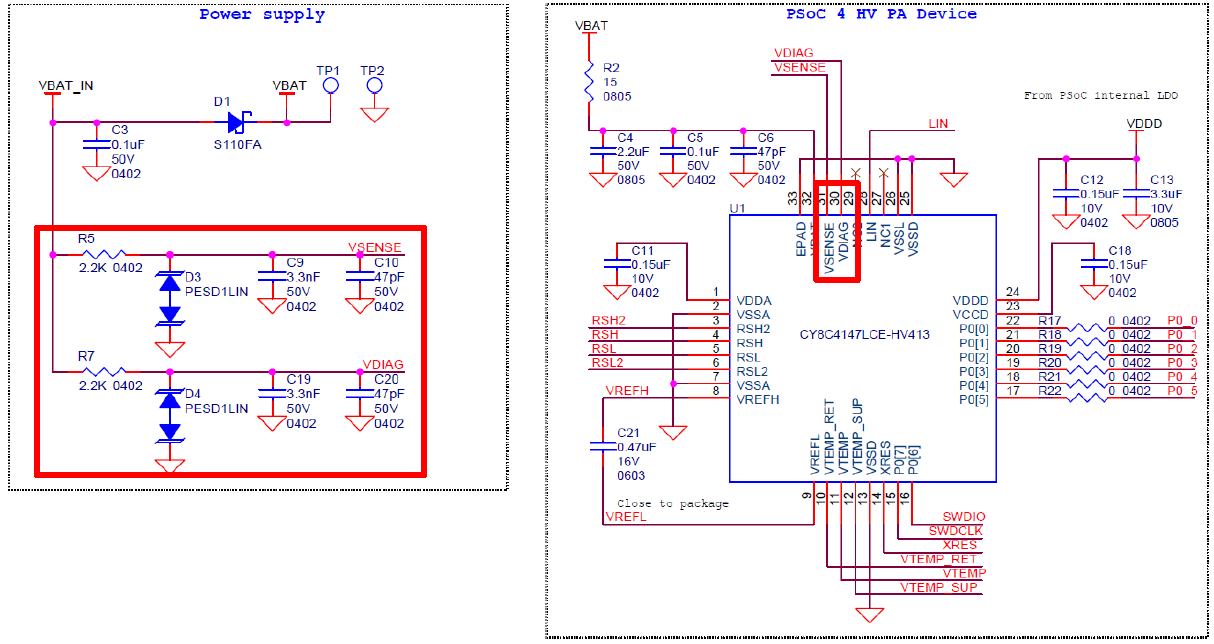
Symbol | Overview | Parameter | ||
---|---|---|---|---|
Value 1 | Value 2 | Remark | ||
R5, R7 | Resistor for the external noise filter | 2.2 kΩ | > 1/10 W | |
D3, D4 | Transient voltage suppressor (TVS) | Bidirectional | Clamping voltage 44 V | Optional |
C9, C19 | Capacitor for the external noise filter | 3.3 nF X7R | > 50 V | |
C10, C20 | Capacitor for the external noise filter | 47 pF C0G | > 50 V |
Note: Resistor values for the voltage path (R5/R7): Note that any deviation from the nominal 2.2 kΩ is associated with a reduction in accuracy.
Layout example
shows an example of the LIN layout.
Figure 10. VDIVIDER layout example
Follow these guidelines for the design of the voltage sensor line circuit on the PSOC™ 4 HV PA device:
Keep the wiring lengths of VSENSE and VDIAG as equal as possible
Wire the VSENSE and VDIAG sensor lines from each VBAT point
Keep the wiring width in the range of 0.127 mm to the IC terminal width
Guard the entire pattern by GND
Place the GND layer under the sensor line
LIN PHY
Schematic example
shows an example of LIN schematic;
Table 13
shows an example of external components.
Figure 11. LIN schematic example
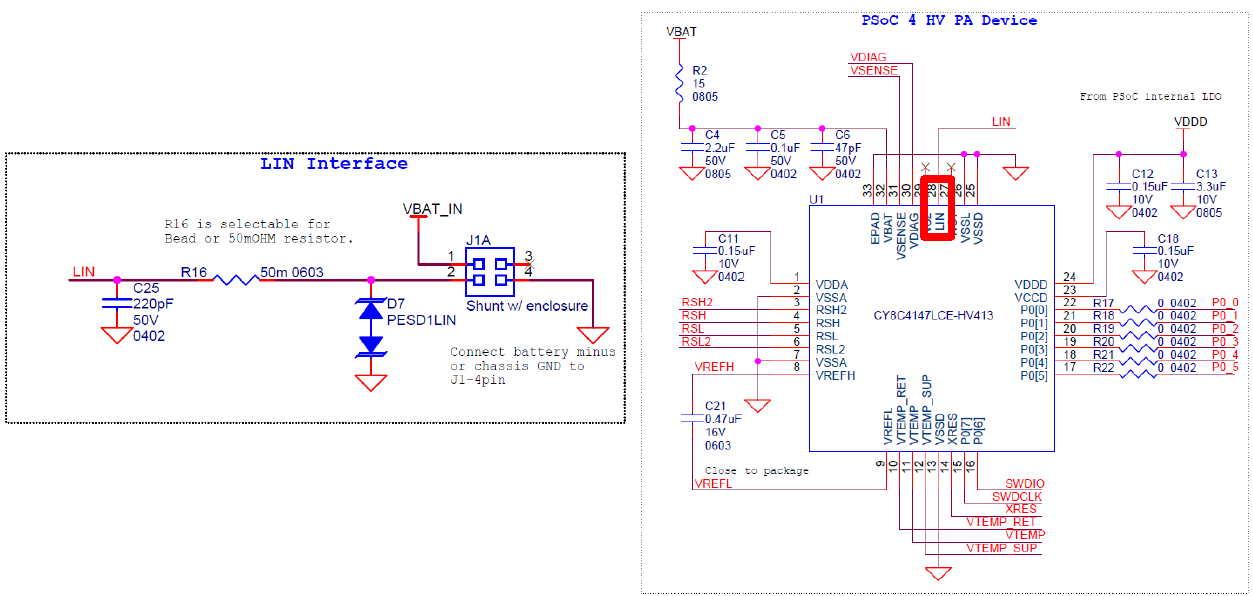
Symbol | Overview | Parameter | ||
---|---|---|---|---|
Value 1 | Value 2 | Remark | ||
C25 | Decoupling capacitor for the LIN domain | 220 pF C0G | > 50 V | |
R16 | Input filter resistance for the high-voltage domain | 50 mΩ | > 1/3 W | |
D7 | Transient voltage suppressor (TVS) diode | Bidirectional | Clamping voltage 44 V |
Layout example
shows an example of the LIN layout.
Figure 12. LIN layout example
Follow these guidelines for the PCB HVSS circuit:
Place capacitor (C25) near the LIN and VSSL terminals
Place the TVS diode (D7) for ESD protection near the LIN connector
Connect the LIN wiring as straight as possible
Change the optional filter element (R16) per your application
Place GND vias near the C25 and D7 terminals
Do not connect VSSL to the EP pad
Place a guard under the LIN wiring with a GND layer
Place a guard around LIN with GND
ESD protection
Electro-static discharge (ESD) events generate high voltages and high currents depending on the path the charge takes to go to ground. If not properly bypassed, the voltages cause immediate oxide dielectric breakdown, especially in advanced geometry technologies with thin gate oxides, creating a weak spot in the oxide which allows the current flow and localized heating.
Depending on the current flow, this could cause permanent damage. A high current flow can cause overheating and melt the silicon, which results in creating a permanent short or high-leakage sites. High currents can also cause junction or metal failure. In summary, ESD failures can be caused by oxide breakdown, junction burnout, or metallization failure.
The following sections describe the ESD protection mechanism for each HVSS block.
HVREG protection
shows the detailed block diagram for HVREG ESD protection. HVREG includes the cascode ESD transistors and two pads for the VBAT pin. The cascode ESD transistors are used to bypass the charge to the ground. Two pads for the VBAT pin reduce the impact by oxide breakdown, junction burnout, or metallization failure due to excess current.
Figure 13. HVREG ESD protection
VDIVIDER protection
shows the detailed block diagram for VDIVIDER ESD protection.
VDIVIDER includes the cascode ESD transistors for
V
SENSE
and
V
DIAG
pins, which are used to bypass the charge to ground. The external 2.2 kΩ resistors in series with the voltage sources limit the current during ESD and transient voltage events.
Figure 14. VDIVIDER ESD protection
LIN PHY protection
shows the detailed block diagram for LIN PHY ESD protection.
LIN PHY includes an HVPMOS diode, cascode ESD transistors, and two pads for the LIN and VSSL pins. The cascode ESD transistors are used to bypass the charge to VSSL. The two pads for the LIN and VSSL pins reduce the impact by oxide breakdown, junction burnout, or metallization failure due to excess current.
Figure 15. LIN PHY ESD protection
ESD events in an uncontrolled environment
Despite the protection element inside the silicon, ESD events in an uncontrolled environment (end-user, retail customer, etc.) can be much more damaging. System design must take ESD protection on the PCB into account to prevent ESD events in the uncontrolled environment. This is usually done through techniques such as ESD protection devices (external devices), PCB layout techniques that attempt to control ESD, and appropriate grounding and shielding techniques.
PSOC™ 4 HV PA requires sufficient protection to withstand high voltage ESD on specific pins. ESD on LIN,
V
BAT
,
V
SENSE
, and
V
DIAG
pins is rated at ±8 kV, and is required to be protected by external devices as shown in
Figure 16
.
Figure 16. External device ESD protection
API details
This chapter describes the APIs in shown
Table 7
. See the
SDL_psoc4hvpaXXXk.chm
file in the
SDL
path below for more information of all PSOC™ 4 HV PA APIs:
C:/<user path>\ PSoC_Sample_Driver_Library_x.x.x\docs
Cy_Hvss_Init()
cy_en_hvss_status_t Cy_Hvss_Init(cy_stc_hvss_config_t *config)
Description:
This function configures the HVSS module, which includes RDIV (resistor attenuation) and LIN-PHY configuration. This function should be called before using LIN communication functions.
Parameters:
config \ref cy_stc_hvss_config_t
Returns:
CY_HVSS_SUCCESS
– HVSS configuration completed successfully
CY_HVSS_BAD_PARAM
– One or more invalid parameters
CY_HVSS_ERROR
– Error occurred while configuring
Cy_Hvss_DeInit()
cy_en_hvss_status_t Cy_Hvss_DeInit(void)
Description:
This function deinitializes both the LIN module and the RDIV.
Parameters:
None.
Returns:
CY_HVSS_SUCCESS
– HVSS configuration completed successfully
CY_HVSS_BAD_PARAM
– One or more invalid parameters
CY_HVSS_ERROR
– Error occurred while configuring
Cy_Hvss_Hvreg_GetStatus()
__STATIC_INLINE uint8_t Cy_Hvss_Hvreg_GetStatus(void)
Description:
This function gets the status of the HVSS regulator.
Parameters:
None.
Returns:
PWR_GOOD
– Status bit.
Cy_Hvss_Rvid_EnableVS0()
__STATIC_INLINE void Cy_Hvss_Rvid_EnableVS0(void)
Description:
This function enables VS0 in RDIV.
Parameters:
None.
Returns:
None.
Cy_Hvss_Rvid_DisableVS0()
__STATIC_INLINE void Cy_Hvss_Rvid_DisableVS0(void)
Description:
This function disables VS0 in resistor attenuator control (RDIV).
Parameters:
None.
Returns:
None.
Cy_Hvss_Rvid_EnableVS1()
__STATIC_INLINE void Cy_Hvss_Rvid_EnableVS1(void)
Description:
This function enables VS1 in resistor attenuator control (RDIV).
Parameters:
None.
Returns:
None.
Cy_Hvss_Rvid_DisableVS1()
__STATIC_INLINE void Cy_Hvss_Rvid_DisableVS1(void)
Description:
This function disables VS1 in resistor attenuator control (RDIV).
Parameters:
None.
Returns:
None.
Cy_Hvss_Rvid_SetPowerMode ()
__STATIC_INLINE void Cy_Hvss_Rvid_SetPowerMode(cy_en_hvss_rdiv_power_mode_type_t mode)
Description:
This function sets the power domain mode in resistor attenuator control (RDIV).
Parameters:
mode \ref cy_en_hvss_rdiv_power_mode_type_t
- CY_HVSS_RDIV_MODE_ACTIVE_DEEPSLEEP = 0
- CY_HVSS_RDIV_MODE_ACTIVE_ONLY = 1
Returns:
None.
Cy_Hvss_Rvid_GetPowerMode
__STATIC_INLINE cy_en_hvss_rdiv_power_mode_type_t Cy_Hvss_Rvid_GetPowerMode(void)
Description:
This function gets then power domain mode of resistor attenuator control (RDIV).
Parameters:
None.
Returns:
\ref cy_en_hvss_rdiv_power_mode_type_t
- CY_HVSS_RDIV_MODE_ACTIVE_DEEPSLEEP = 0
- CY_HVSS_RDIV_MODE_ACTIVE_ONLY = 1
Cy_Hvss_Rvid_SetAttenuationVS0
__STATIC_INLINE void Cy_Hvss_Rvid_SetAttenuationVS0(cy_en_hvss_rdiv_attenuation_type_t attenuation)
Description:
This function gets the VS0 attenuation of resistor attenuator control (RDIV).
Parameters:
mode \ref cy_en_hvss_rdiv_attenuation_type_t
- CY_HVSS_RDIV_ATTENUATION_16X = 0
- CY_HVSS_RDIV_ATTENUATION_24X = 1
Returns:
None.
Cy_Hvss_Rvid_GetAttenuationVS0
__STATIC_INLINE cy_en_hvss_rdiv_attenuation_type_t Cy_Hvss_Rvid_GetAttenuationVS0(void)
Description:
This function gets the VS0 attenuation of resistor attenuator control (RDIV).
Parameters:
None.
Returns:
\ref cy_en_hvss_rdiv_attenuation_type_t
- CY_HVSS_RDIV_ATTENUATION_16X = 0
- CY_HVSS_RDIV_ATTENUATION_24X = 1
Cy_Hvss_Rvid_SetAttenuationVS1
__STATIC_INLINE void Cy_Hvss_Rvid_SetAttenuationVS1(cy_en_hvss_rdiv_attenuation_type_t attenuation)
Description:
This function gets the VS1 attenuation of resistor attenuator control (RDIV).
Parameters:
mode \ref cy_en_hvss_rdiv_attenuation_type_t
- CY_HVSS_RDIV_ATTENUATION_16X = 0
- CY_HVSS_RDIV_ATTENUATION_24X = 1
Returns:
None.
Cy_Hvss_Rvid_GetAttenuationVS1
__STATIC_INLINE cy_en_hvss_rdiv_attenuation_type_t Cy_Hvss_Rvid_GetAttenuationVS1(void)
Description:
This function gets the VS1 attenuation of resistor attenuator control (RDIV).
Parameters:
None.
Returns:
\ref cy_en_hvss_rdiv_attenuation_type_t
- CY_HVSS_RDIV_ATTENUATION_16X = 0
- CY_HVSS_RDIV_ATTENUATION_24X = 1
Cy_Hvss_LinPhy_SetRxdPin
__STATIC_INLINE void Cy_Hvss_LinPhy_SetRxdPin(uint8_t status)
Description:
This function sets the status of the LIN-PHY RxD pin.
Parameters:
status lin
– RxD pin status (HIGH or LOW).
Returns:
None.
Cy_Hvss_LinPhy_GetRxdPin
__STATIC_INLINE uint8_t Cy_Hvss_LinPhy_GetRxdPin(void)
Description:
This function gets the status of the LIN-PHY, which indicates the current status of the LIN RxD pin.
Parameters:
None.
Returns:
uint8_t
– Status of the LIN-PHY.
Cy_Hvss_LinPhy_EnableWakeupTimer
__STATIC_INLINE void Cy_Hvss_LinPhy_EnableWakeupTimer(void)
Description:
This function enables the LIN-PHY wake-up timer, which is required in DS mode for LIN compatibility.
Parameters:
None.
Returns:
None.
Cy_Hvss_LinPhy_DisableWakeupTimer
__STATIC_INLINE void Cy_Hvss_LinPhy_DisableWakeupTimer(void)
Description:
This function disables the LIN-PHY wake-up timer.
Parameters:
None.
Returns:
None.
Cy_Hvss_LinPhy_GetWakeupTimerStatus
__STATIC_INLINE uint16_t Cy_Hvss_LinPhy_GetWakeupTimerStatus(void)
Description:
This function gets the status of the LIN-PHY wakeup timer, which indicates the timer count if running.
Parameters:
None.
Returns:
uint16_t
– Status of the LIN-PHY wakeup timer.
Cy_Hvss_LinPhy_EnableFaultTimer
__STATIC_INLINE void Cy_Hvss_LinPhy_EnableFaultTimer(void)
Description:
This function enables the LIN-PHY fault timer, which is required LIN for compatibility in DS mode.
Parameters:
None.
Returns:
None.
Cy_Hvss_LinPhy_DisableFaultTimer
__STATIC_INLINE void Cy_Hvss_LinPhy_DisableFaultTimer(void)
Description:
This function disables the LIN-PHY fault timer.
Parameters:
None.
Returns:
None.
Cy_Hvss_LinPhy_GetFaultTimerStatus
__STATIC_INLINE uint16_t Cy_Hvss_LinPhy_GetFaultTimerStatus(void)
Description:
This function gets the status of the LIN-PHY fault timer, which provides the timer count if running.
Parameters:
None.
Returns:
uint16_t
– Status of the LIN-PHY fault timer.
Cy_Hvss_LinPhy_SetPhyMode
__STATIC_INLINE void Cy_Hvss_LinPhy_SetPhyMode(cy_en_hvss_lin_phy_mode_type_t mode)
Description:
This function sets the mode of the LIN-PHY.
Parameters:
mode /ref cy_en_hvss_lin_phy_mode_type_t
- CY_HVSS_LIN_PHY_MODE_DISABLED = 0
- CY_HVSS_LIN_PHY_MODE_SLEEP = 1
- CY_HVSS_LIN_PHY_MODE_STANDBY = 2
- CY_HVSS_LIN_PHY_MODE_DIAGNOSIS = 3
- CY_HVSS_LIN_PHY_MODE_NORMAL_1_0 = 4
- CY_HVSS_LIN_PHY_MODE_NORMAL_1_5 = 5
- CY_HVSS_LIN_PHY_MODE_NORMAL_2_0 = 6
- CY_HVSS_LIN_PHY_MODE_FAST = 7
Returns:
None
Cy_Hvss_LinPhy_GetPhyMode
__STATIC_INLINE cy_en_hvss_lin_phy_mode_type_t Cy_Hvss_LinPhy_GetPhyMode(void)
Description:
This function gets the current mode of the LIN-PHY.
Parameters:
None.
Returns:
/ref cy_en_hvss_lin_phy_mode_type_t
- CY_HVSS_LIN_PHY_MODE_DISABLED = 0
- CY_HVSS_LIN_PHY_MODE_SLEEP = 1
- CY_HVSS_LIN_PHY_MODE_STANDBY = 2
- CY_HVSS_LIN_PHY_MODE_DIAGNOSIS = 3
- CY_HVSS_LIN_PHY_MODE_NORMAL_1_0 = 4
- CY_HVSS_LIN_PHY_MODE_NORMAL_1_5 = 5
- CY_HVSS_LIN_PHY_MODE_NORMAL_2_0 = 6
- CY_HVSS_LIN_PHY_MODE_FAST = 7
Cy_Hvss_LinPhy_SetPhySlRound
__STATIC_INLINE void Cy_Hvss_LinPhy_SetPhySlRound(cy_en_hvss_lin_phy_emi_type_t mode)
Description:
This function sets the SL round value of the LIN-PHY for lower EMI.
Parameters:
mode /ref cy_en_hvss_LinPhy_emi_type_t
- CY_HVSS_LIN_PHY_SL_ROUND_NORMAL = 0
- CY_HVSS_LIN_PHY_SL_ROUND_MODERATE = 1
Returns:
None.
Cy_Hvss_LinPhy_GetPhySlRound
__STATIC_INLINE cy_en_hvss_lin_phy_emi_type_t Cy_Hvss_LinPhy_GetPhySlRound(void)
Description:
This function gets the SL round mode of the LIN-PHY.
Parameters:
None.
Returns:
/ref cy_en_hvss_LinPhy_emi_type_t
- CY_HVSS_LIN_PHY_SL_ROUND_NORMAL = 0
- CY_HVSS_LIN_PHY_SL_ROUND_MODERATE = 1
Cy_Hvss_LinPhy_SetPhyInterface
__STATIC_INLINE void Cy_Hvss_LinPhy_SetPhyInterface(cy_en_hvss_lin_phy_interface_type_t mode)
Description:
This function sets the internal or GPIO connection of the LIN-PHY through the HSIOM.
Parameters:
/ref cy_en_hvss_LinPhy_interface_type_t
- CY_HVSS_LIN_PHY_INTERFACE_PRIMARY = 0
- CY_HVSS_LIN_PHY_INTERFACE_SECONDARY = 1
Returns:
None.
Cy_Hvss_LinPhy_GetPhyInterface
__STATIC_INLINE cy_en_hvss_lin_phy_interface_type_t Cy_Hvss_LinPhy_GetPhyInterface(void)
Description:
This function gets the connection interface of the LIN-PHY through internal or GPIO.
Parameters:
None.
Returns:
/ref cy_en_hvss_LinPhy_interface_type_t
- CY_HVSS_LIN_PHY_INTERFACE_PRIMARY = 0
- CY_HVSS_LIN_PHY_INTERFACE_SECONDARY = 1
Cy_Hvss_LinPhy_EnablePhy
__STATIC_INLINE void Cy_Hvss_LinPhy_EnablePhy(void)
Description:
This function enables the LIN-PHY.
Parameters:
None.
Returns:
None.
Cy_Hvss_LinPhy_DisablePhy
__STATIC_INLINE void Cy_Hvss_LinPhy_DisablePhy(void)
Description:
This function disables the LIN-PHY.
Parameters:
None.
Returns:
None.
Cy_Hvss_LinPhy_GetPhyStatus
__STATIC_INLINE uint8_t Cy_Hvss_LinPhy_GetPhyStatus(void)
Description:
This function gets the status of the LIN-PHY.
1: Enabled
0: Reset (RxD pin is High-Z)
Parameters:
None.
Returns:
uint8_t
– Status of the LIN-PHY.
Cy_Hvss_LinPhy_ClearInterrupt
__STATIC_INLINE void Cy_Hvss_LinPhy_ClearInterrupt(uint32_t interrupt)
Description:
This function clears the interrupt from the LIN_INTR register.
Parameters:
interrupt – Interrupt mask for the interrupt.
Returns:
None.
Cy_Hvss_LinPhy_SetInterrupt
__STATIC_INLINE void Cy_Hvss_LinPhy_SetInterrupt(uint32_t interrupt)
Description:
This function sets the interrupt in the LIN_INTR register.
Parameters:
interrupt
– Interrupt mask for the interrupt.
Returns:
None.
Cy_Hvss_LinPhy_GetInterruptMask
__STATIC_INLINE uint32_t Cy_Hvss_LinPhy_GetInterruptMask(void)
Description:
This function returns the interrupt mask from the LIN_INTR_MASK register.
Parameters:
None.
Returns:
uint32_t
–Interrupt bit mask.
Cy_Hvss_LinPhy_SetInterruptMask
__STATIC_INLINE void Cy_Hvss_LinPhy_SetInterruptMask(uint32_t interrupt)
Description:
This function sets the interrupt mask in the LIN_INTR_MASK register.
Parameters:
interrupt
– Interrupt mask for the interrupt.
Returns:
None.
Cy_Hvss_LinPhy_GetInterruptStatusMasked
__STATIC_INLINE uint32_t Cy_Hvss_LinPhy_GetInterruptStatusMasked(void)
Description:
This function returns the masked status from the LIN_INTR_MASKED register.
Parameters:
None.
Returns:
Interrupt bit mask(s).
Cy_Hvss_LinPhy_SetWakeupInterruptMask
__STATIC_INLINE void Cy_Hvss_LinPhy_SetWakeupInterruptMask(void)
Description:
This function sets the wakeup interrupt status masked in the LIN_INTR_MASK register.
Parameters:
None.
Returns:
None.
Cy_Hvss_LinPhy_ClearWakeupInterruptMask
__STATIC_INLINE void Cy_Hvss_LinPhy_ClearWakeupInterruptMask(void)
Description:
This function clears the wakeup interrupt status masked in the LIN_INTR_MASK register.
Parameters:
None.
Returns:
None.
Cy_Hvss_LinPhy_SetFaultInterruptMask
__STATIC_INLINE void Cy_Hvss_LinPhy_SetFaultInterruptMask(void)
Description:
This function sets the fault interrupt status masked in the
LIN_INTR_MASK
register.
Parameters:
None.
Returns:
None.
Cy_Hvss_LinPhy_ClearFaultInterruptMask
__STATIC_INLINE void Cy_Hvss_LinPhy_ClearFaultInterruptMask(void)
Description:
This function clears the fault interrupt status masked in the
LIN_INTR_MASK
register.
Parameters:
None.
Returns:
None.
Summary
This application note guides you through the details of the high-voltage subsystem of PSOC™ 4 HV PA, enabling you to connect automotive batteries directly and achieve battery monitoring and management applications with a minimal number of external components. Infineon provides evaluation boards and a wealth of sample software to help you get started with the PSOC™ 4 HV PA family. To access the evaluation board, contact your sales representative or reach out to
Infineon Technical Support
.
Glossary
Terms | Description |
---|---|
A/D converter | analog to digital converter |
ADC | analog to digital converter |
AHB | advanced high-performance bus |
API | application programming interface |
BOD | brown-out detectors |
CPU | central processing unit |
CPUSS | CPU sub-system |
DAP | debug access port |
DC | direct current |
DMA | direct memory access |
DMAC | DMA controller |
DW | data wire |
ECC | error correction code (safety) |
ECU | electronic control unit |
EM | electro-magnetic |
EMI | electro-magnetic interference |
ESD | electro-static discharge |
GPIO | general purpose I/O |
HSIOM | high-speed I/O matrix |
HVREG | high-voltage regulator |
HVSS | high-voltage subsystem |
I/O | input or output |
IOSS | I/O subsystem |
IRC | interrupt controller |
IRQ | interrupt request |
ISR | interrupt service routine |
LIN | local interconnect network |
MCU | microcontroller unit |
MPU | memory protection unit |
NMI | non-maskable interrupt |
PA | precision analog |
PACSS | precision analog channel subsystem |
PCB | printed circuit board |
PG | power good |
PHY | physical interface transceiver |
POR | power on reset |
PWM | pulse width modulation |
RAM | random access memory |
RDIV | resistor attenuator control |
RF | radio frequency |
ROM | read-only memory |
SCB | serial communication block |
SDL | sample driver library |
SPI | serial peripheral interface |
SRAM | static RAM |
SRSS | system resource sub-system |
TCPWM | timer, counter and PWM |
TRM | technical reference manual |
TVS | transient voltage suppressor |
VDIVIDER | voltage divider |
WDT | watchdog timer |
References
The following are the PSOC™ 4 HV PA family series application notes, datasheets and technical reference manuals. Contact
Technical Support
to obtain these documents and sample driver library.
Application notes
AN230264 - Getting started with PSOC™ 4 HV PA family
AN230265 - Hardware design guide for PSOC™ 4 HV PA family
AN230370 - Precision analog channel subsystem in PSOC™ 4 HV PA family
Device datasheet
PSOC™ 4 HV precision analog datasheet
Architecture reference manual
PSOC™ 4 HV PA architecture reference manual (RM)
Registers reference manual
PSOC™ 4 HV PA registers reference manual (RM)
Evaluation board user guide
PSOC™ 4 HV PA evaluation board user guide
Sample driver library (SDL)
PSOC™ 4 HV PA sample driver library
Revision history
Document revision | Date | Description of changes |
---|---|---|
** | 2021-11-22 | Initial release |
*A | 2023-04-19 | Template update; no content updated. |
*B | 2024-11-20 | Updated to the latest branding guidelines Sunset review complete |